A Guide to CNC Bits
Choosing bits to use for your CNC router may be confusing. There are many variables to consider when looking for the perfect CNC router bit for your project, we have provided some points to consider when purchasing your CNC router bits.
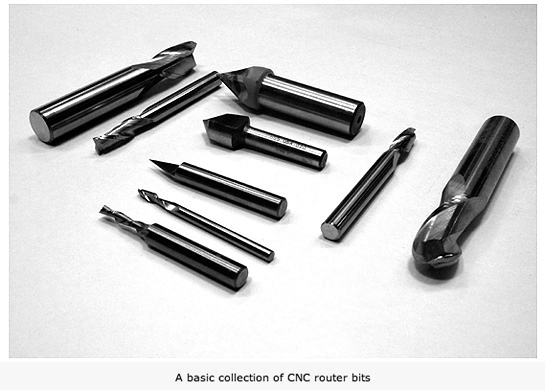
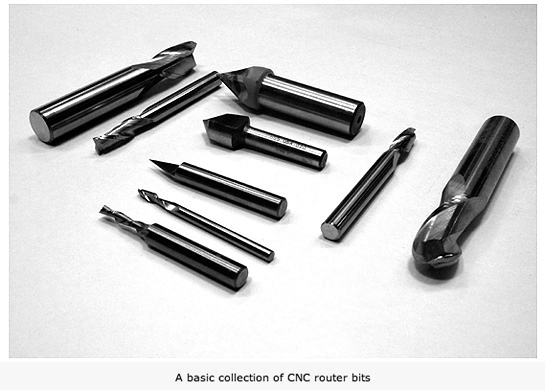
1) Choose the bit shape suited for your project


Are you making straight cuts in plywood? Get yourself a good quality solid carbide spiral, available in upcut or downcut.
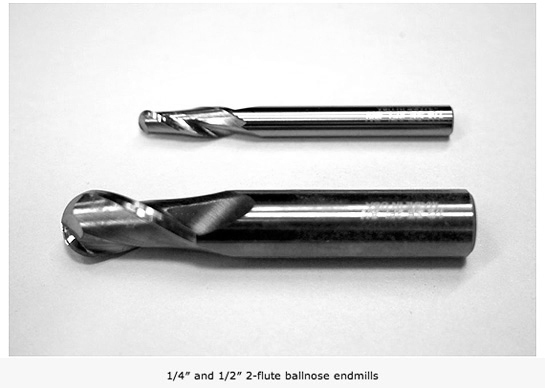
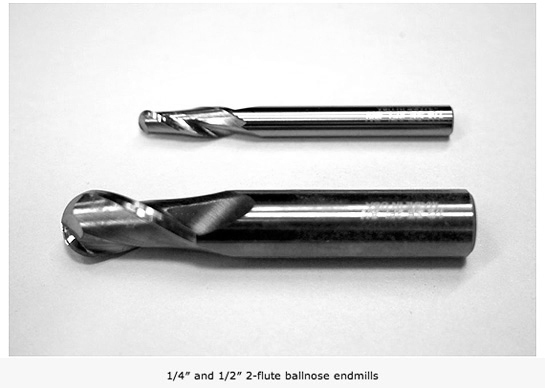
Are you carving large 3D carvings? You’ll want a ball nose bit that is appropriately sized for the level of detail in your model.
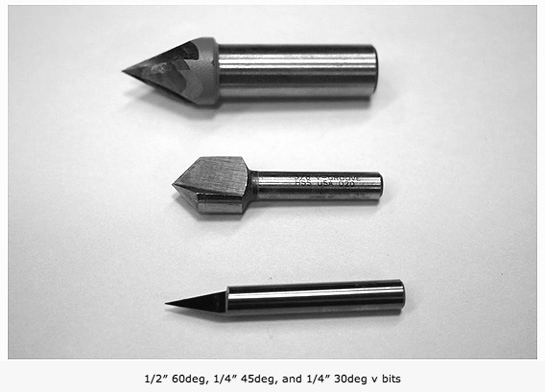
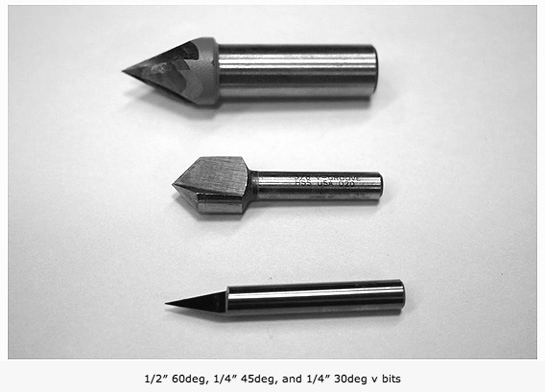
If you want to create lettering and or signmaking, you’ll need to get a v-groove router bit. This is the only way to get a sharp grooves on your workpiece. They are available in many sizes and angles.
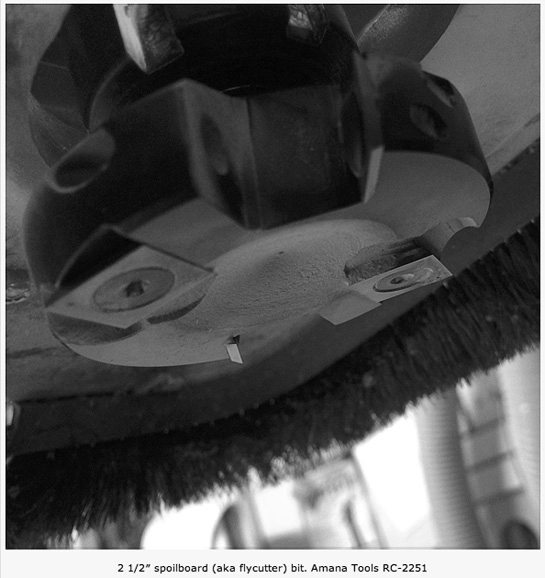
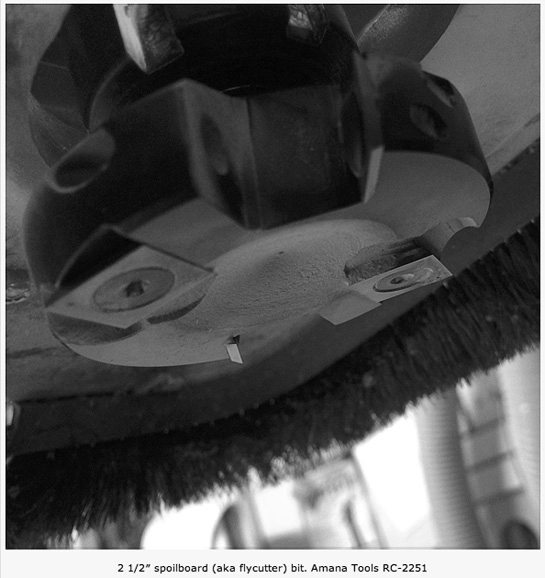
If you are flattening large boards or you are responsible for maintaining the spoil board on your CNC router, you’ll want to have a spoil board cutter. These bits are made to skim the surface and leave a smooth flat finish. I recently upgraded to a 2-1/2″ Amana Tool #RC-2251 bit and I love it. Its got four cutting edges and its what as known as an “insert” bit meaning the blades can be removed to be resharpened or replaced.
2) Choose a bit made for your material.
Each type of material such as hardwood, plywood, plastic, aluminum, MDF and more, each require a specific type of router bit, be sure to check the specifications of the bit type when purchasing your bits.
3) Use the strongest bit you can
Generally shorter bits produce cleaner cuts. Having extremely long bits opens the door for tool vibration and the possibility of bending the bit. Both of these conditions make for rough looking cuts and greatly shortened tool life.
4) Balance your need for speed with edge finish
The bit design you choose will be designed to cut fast or cut smooth. If you need to cut a large amount of material in a hurry or in a high production environment you should choose an aggressive bit that can be pushed through your material quickly.
5) Choose the appropriate bit direction
Spiral bits are excellent multipurpose toosl for many applications. The biggest decision you’ll need to make when picking your bit is cut direction. Your choice are uncut, downcut, and compression (a combination of upcut and downcut).
Upcut bits mounted in a CNC pull chips (and your material) up and away from the table while downcut bits press chips and material back into the cut and into the table.
6) Setting feeds and speeds
Feedrate refers to how fast the machine moves laterally through your material while Speeds are referring to the spindle/router RPM. Chipload=Feedrate/[RPM x number of flutes]
7) Storing your bits
Protect your investment! Be sure the edges of your bits aren’t allowed to bang into each other causing nicks.
Originally posted by Greg from Tinker and Futz on March 11th, 2014 Here