Advanced CNC Joinery Techniques
By combining the precision of CNC technology with traditional joinery knowledge, modern woodworkers can unlock new levels of strength, creativity, and efficiency.
How CNC Joinery Differs from Traditional Techniques
Traditional woodworking relies on hand tools or stationary machines like table saws and mortisers to create joints with square, sharp inside corners. For example, a classic mortise and tenon joint is designed with crisp 90° angles throughout.
But CNC routers use rotating bits—and round bits can't cut sharp inside corners. This means that when you try to machine a perfect square pocket or mortise on a CNC, the internal corners end up rounded. If you try to fit a square tenon into that space, it simply won’t seat properly.
That’s where CNC-specific joints like the Dogbone Joint come in.
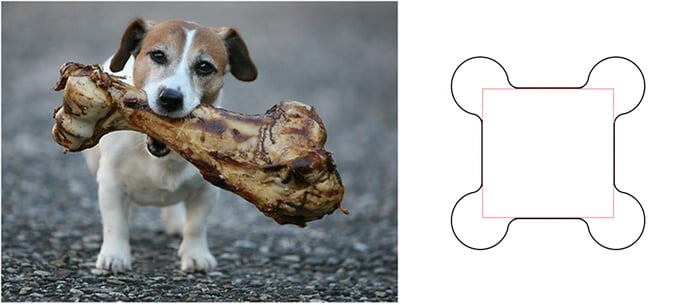
What is a DogBone Joint?
A Dogbone Joint is a CNC-friendly adaptation that solves the inside-corner problem. It involves extending a small circular relief—shaped like a dog bone—at each inside corner of the pocket or slot. This extra cut allows square-edged parts to fully seat without interference from the bit’s radius.
The result isn’t just a functional solution—it also gives CNC joinery a distinct visual character, often associated with flat-pack furniture and modern fabrication methods. You’ll see this approach used heavily in cabinetry, modular shelving, and anything designed for CNC-based assembly.
Now let’s explore the advanced joints and techniques that take your CNC work from functional to exceptional.
Why CNC Joinery Is a Game-Changer
- Precision: CNC machines produce exact cuts down to fractions of a millimeter, ensuring tight-fitting joints every time.
- Repeatability: Once programmed, a CNC can produce hundreds of identical components with no variation.
- Complexity Made Simple: Intricate joints like dogbones, T-bones, or sliding dovetails are easy to produce with the right setup.
- Efficiency: CNC joinery dramatically reduces manual labor, speeds up production, and minimizes waste.
- Creativity: You’re no longer limited by the physical constraints of traditional tools—CNC frees you to design joints for form and function.
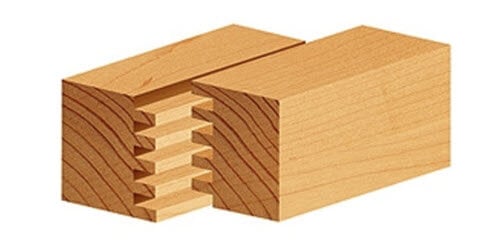
Types of CNC Wood Joints: A Comparative Guide
Joint Type | Strength | Common Uses | Machining Difficulty | Aesthetic Appeal | Pro Tip |
---|---|---|---|---|---|
Box Joint | High | Drawers, boxes, casework | Moderate | Visible grid pattern | Adjust finger size for wood thickness; tolerance matters! |
Blind Box Joint | High | Drawers with clean exteriors | Advanced | Seamless outer edge | Great for face-frame cabinetry—requires tight tolerances |
Dogbone Joint | Medium | Flat-pack furniture | Easy | Tech-industrial look | Ensure inside fillets are larger than your bit radius |
T-Bone Joint | Medium | Fast fixtures, modular projects | Easy | Functional, not fancy | Good option when tight corners are needed for slots |
Housing Joint (Dado) | Medium | Bookshelves, dividers | Easy | Hidden | Leave 0.1 mm of clearance to account for glue swell |
Step Joint | Very High | Structural frames, heavy furniture | Advanced | Hidden or subtle | Good for wide glue surface and strong interlocking |
Design Considerations That Matter
- Finger Size: In box joints, finger width should be at least twice your endmill diameter to avoid weakening the structure.
- Fillet Radius: Dogbone and T-bone fillets must accommodate your bit radius—don’t undershoot or the joints won’t fit.
- Overlap and Surface Area: For step joints and housing joints, maximize glue surface to improve strength.
Real-World Applications by Joint Type
- Box Joints: Perfect for batch-producing small drawer boxes or speaker enclosures where uniformity matters.
- Dogbone Joints: Ideal for furniture that needs to be assembled/disassembled repeatedly—think pop-up kiosks or modular shelves.
- Step Joints: Excellent for architectural millwork and thick stock furniture requiring hidden reinforcement.
Common Pitfalls (and How to Avoid Them)
- Undersized Fillets: Corners won’t seat properly. Use a fillet radius at least 1.1× your tool radius.
- Loose Fits: CNC tolerances must account for bit wear and finishing passes. Use scrap to dial in fit before production.
- Overclamping: Especially with housing joints, overclamping during glue-up can distort alignment—use cauls and a flat reference surface.
- Fixturing Errors: If your stock shifts during machining, your joints won’t align. Use vacuum tables or multiple clamps to keep parts secure.
Choosing the Right CNC Machine for Joinery
Not all CNC machines are ideal for joinery. Here’s what to look for:
- Bed Size: A 4’x8’ bed is ideal for cabinetmakers and large format projects; desktop CNCs can still handle joinery for small boxes and drawers.
- Spindle Power: 2.2kW or greater is recommended for hardwood joinery to maintain clean cuts at high feed rates.
- Tool Compatibility: Look for machines that support tool changers and use common 1/4" and 1/2" shank bits for joinery.
Fixturing and Workpiece Handling Tips
- Secure Every Cut: Use vacuum pods or mechanical clamps to prevent part shift, especially during profile cuts.
- Zero with Care: Calibrate your Z-height from the material surface if using variable-thickness boards.
- Account for Kerf: Always factor in the bit diameter and path mode (inside, outside, on-path) when designing joints.
Final Thoughts
Advanced CNC joinery isn’t just about knowing which joints to cut—it's about understanding how material properties, machine limitations, and design intent work together. By mastering both the techniques and the design strategies behind CNC joinery, you’ll open up new opportunities to build faster, stronger, and more beautifully than ever before.
Bonus: Check out Matt's downloadable, customizable CNC Workbench Plans available now.
FAQs
What types of joints can be made with a CNC machine?
CNC machines can create a wide variety of joints, including box joints, dovetails, blind box joints, dogbone and T-bone joints, housing (dado) joints, and step joints. With the right design and tooling, CNC routers can handle everything from simple butt joints to complex interlocking joinery.
How accurate are CNC machines for joinery?
Modern CNC machines offer incredible accuracy, often within 0.001 inches (0.025 mm), which is more than sufficient for tight-fitting wood joints. However, accuracy also depends on tool sharpness, fixturing, and proper calibration.
Can I use a desktop CNC for joinery, or do I need an industrial machine?
You can absolutely use a desktop CNC for small-scale joinery, such as boxes, drawers, and small furniture. For larger pieces or production work, a full-size or industrial CNC machine is recommended due to increased rigidity and bed size.
What’s the best CNC joint for strength?
Step joints and box joints are among the strongest for CNC woodworking. Step joints offer a large glue surface and mechanical interlock, while box joints distribute stress across multiple fingers, making them ideal for load-bearing applications.
How do I avoid fit issues with CNC joints?
Always test your joint designs on scrap material first. Account for tool deflection, bit wear, and actual vs. nominal bit sizes. Designing joints with a slight tolerance (around 0.1 mm) often resolves tight or loose fits.